200L Industrial Batch Fermentation Bioreactor for Microbiology: Revolutionizing Microbial Production Processes
- Share
- Issue Time
- Jul 22,2024
Summary
200L Industrial Batch Fermentation Bioreactor for Microbiology: Revolutionizing Microbial Production Processes
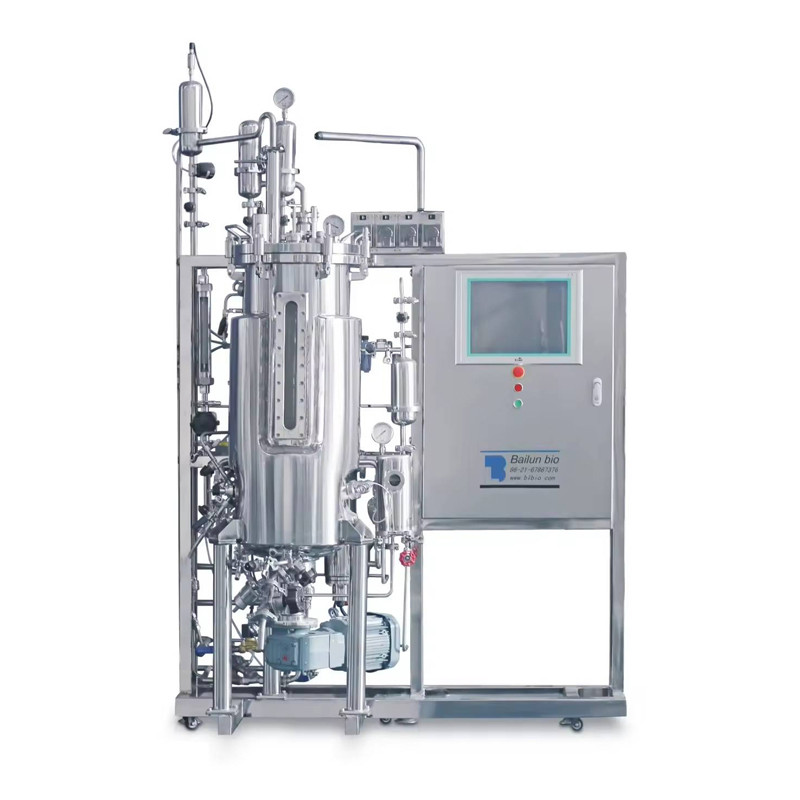
In the dynamic field of microbiology and industrial biotechnology, the 200L industrial batch fermentation bioreactor has emerged as a critical tool, transforming the landscape of microbial production and research. This article explores the various aspects of this bioreactor, including its design, functionality, applications, and the impact it has on advancing microbiological processes.
The design of the 200L industrial batch fermentation bioreactor is a meticulous engineering feat that combines precision and functionality. The vessel is constructed from materials that offer durability, chemical resistance, and the ability to withstand the rigors of industrial-scale operations. Stainless steel is often the material of choice due to its excellent properties in these regards.
The internal configuration of the bioreactor is optimized to ensure efficient mixing and mass transfer. Agitators, typically in the form of impellers, are strategically placed to create a uniform distribution of nutrients, oxygen, and other essential components throughout the 200L volume. The design of the agitation system takes into account factors such as the viscosity of the culture medium and the specific requirements of the microbial species being cultivated.
Temperature control is a crucial aspect of the bioreactor's design. Jackets or coils surrounding the vessel allow for the circulation of heating or cooling fluids, enabling precise maintenance of the desired temperature range. This is vital as different microorganisms have specific temperature optima for growth and metabolic activities.
Aeration is another key component. Specialized devices, such as spargers or membrane oxygenators, are incorporated to supply an adequate amount of oxygen to the microbial culture. The rate of aeration is carefully controlled to meet the oxygen demands of the microorganisms without causing excessive foaming or oxygen toxicity.
The functionality of the 200L industrial batch fermentation 100l bioreactor lies in its ability to provide a controlled and reproducible environment for microbial growth and product formation. This controlled environment allows for precise manipulation of parameters such as pH, dissolved oxygen, and nutrient concentrations.
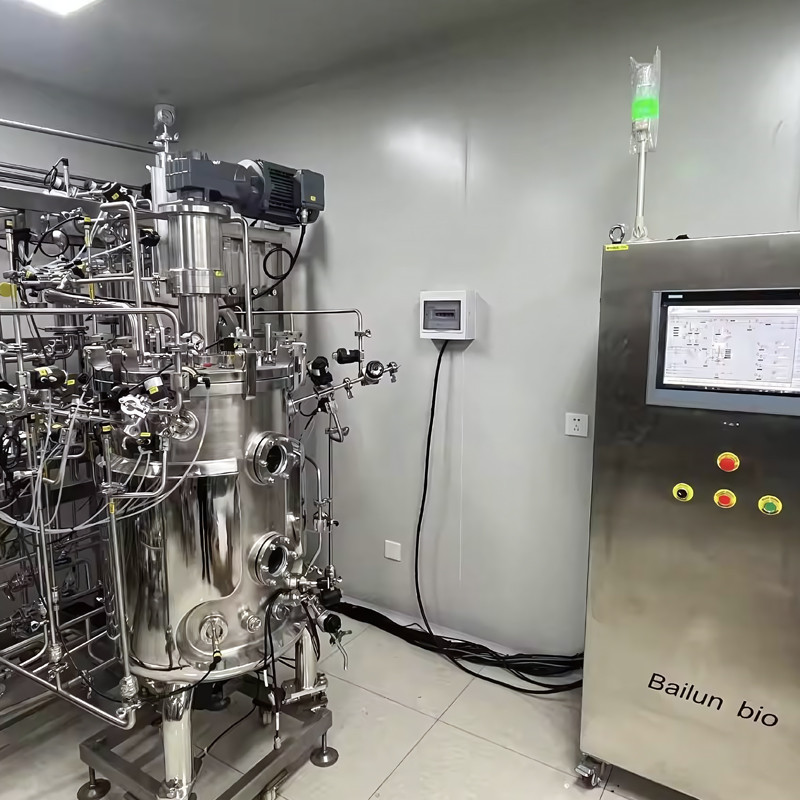
Sensors and monitoring systems continuously measure these parameters, and the data is fed into a control system that enables automatic adjustments to maintain optimal conditions.
One of the significant advantages of the batch fermentation process in this bioreactor is its simplicity and ease of operation. It involves inoculating the bioreactor with a known quantity of microorganisms and providing them with a defined set of nutrients and conditions for a specific period until the desired endpoint is reached.
This makes it suitable for a wide range of applications, especially when a single batch of a product is required or when the process involves complex metabolic pathways that need to be completed within a defined time frame.
The 200L capacity of the bioreactor strikes a balance between scalability and operational flexibility. It is large enough to produce significant quantities of microbial products for industrial purposes while still allowing for relatively manageable setup and monitoring compared to even larger-scale systems.
The applications of the 200L industrial batch fermentation bioreactor in microbiology are vast and diverse. In the production of antibiotics, for example, it enables the cultivation of specific microbial strains that produce these valuable therapeutic compounds. The controlled environment ensures consistent quality and yield of the antibiotics, meeting the strict standards of the pharmaceutical industry.
In the field of enzyme production, the bioreactor provides an ideal platform for microorganisms to express and secrete enzymes in high quantities. These enzymes find applications in various industries, including food processing, textiles, and detergents.
The bioreactor also plays a crucial role in the development of microbial-based biofuels. Microorganisms are grown and metabolically engineered to convert renewable feedstocks into bioethanol, biodiesel, or other alternative fuels. The 200L scale allows for experimentation and optimization of the process before potential scale-up to larger production facilities.
In addition to production processes, the bioreactor is valuable for research and development in microbiology. It enables scientists to study the growth kinetics, metabolic pathways, and physiological responses of microorganisms under controlled conditions. This knowledge is essential for advancing our understanding of microbial behavior and for developing more efficient and sustainable bioprocesses.
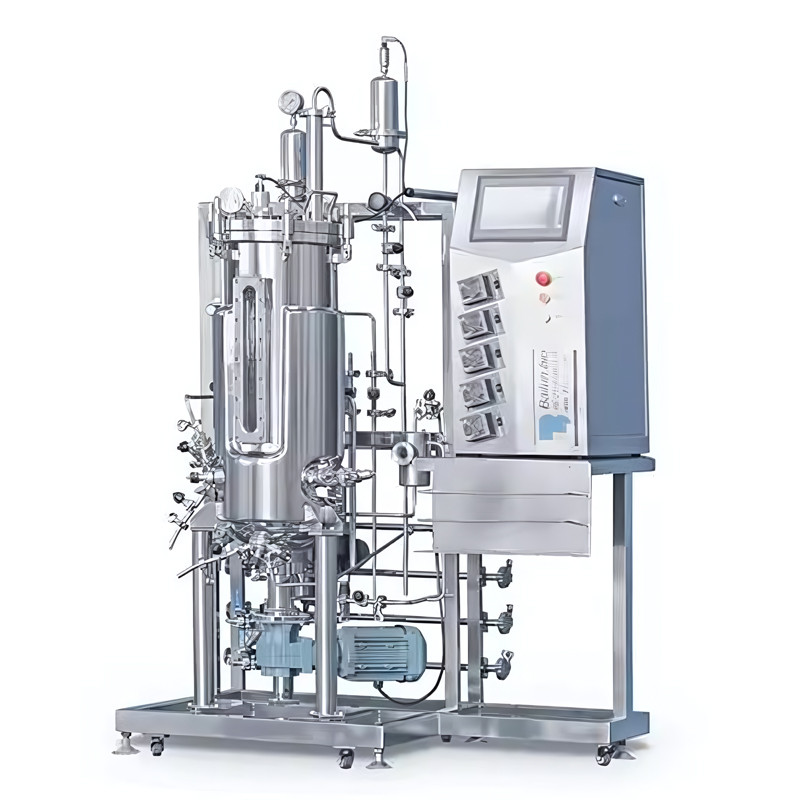
However, operating a 200L industrial batch fermentation bioreactor comes with its challenges. Maintaining sterility throughout the process is of utmost importance to prevent contamination, which could lead to batch failure and significant economic losses. Regular maintenance and calibration of sensors and control systems are necessary to ensure accurate and reliable operation.
Scaling up from laboratory-scale experiments to the 200L industrial scale often requires careful optimization of process parameters. Changes in fluid dynamics, heat transfer, and mass transfer can have significant effects on microbial growth and product formation, and these need to be accounted for during the scale-up process.
Looking forward, the future of the 200L industrial batch fermentation bioreactor holds great promise. Advances in sensor technology, process control algorithms, and materials science are expected to further enhance its performance and efficiency. Integration with artificial intelligence and machine learning techniques could enable predictive analytics and optimization of the fermentation process, leading to higher yields and reduced production costs.
In conclusion, the 200L industrial batch fermentation bioreactor for microbiology is a powerful tool that has revolutionized the way we produce microbial products and conduct microbiological research. Its ability to provide a controlled and scalable environment for microbial growth and metabolism has opened up new possibilities in various industries and has the potential to continue driving innovation and progress in the field of microbiology and biotechnology.