Pharma Manufacturing Bioreactor: Revolutionizing Drug Production with Advanced Technologies
- Share
- Issue Time
- Jun 28,2024
Summary
Pharma Manufacturing Bioreactor: Revolutionizing Drug Production with Advanced Technologies
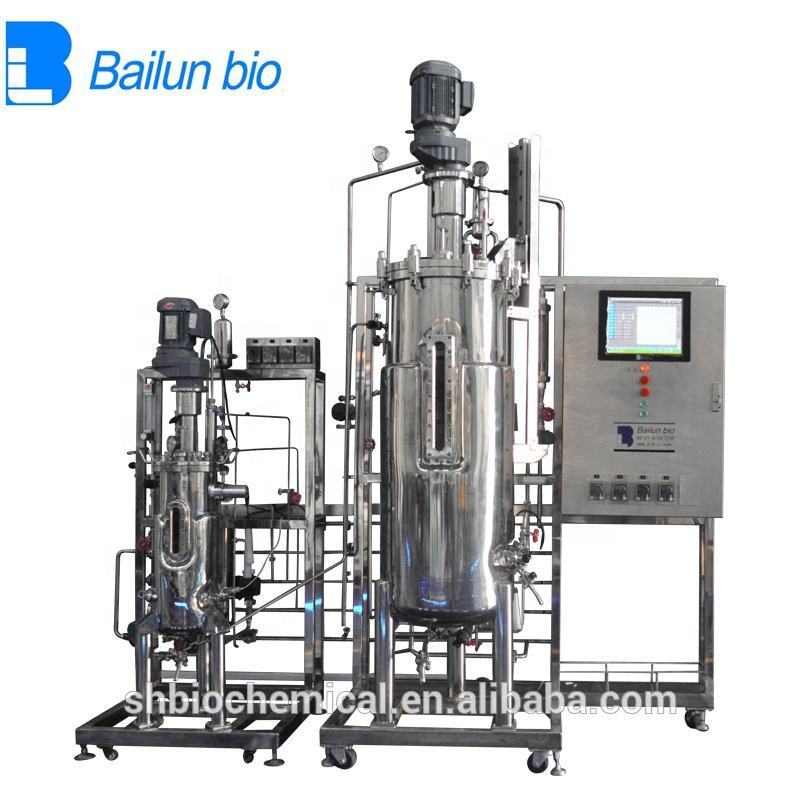
In the ever-evolving landscape of pharmaceutical manufacturing, the role of advanced bioreactors, such as the 200 Liter Stainless Conical Fermenter with a perfusion system, has become increasingly crucial. These cutting-edge technologies are not only transforming the way drugs are produced but also raising the bar for quality, efficiency, and innovation in the pharmaceutical industry.
The 200 Liter Stainless Conical Fermenter represents a significant advancement in bioreactor design. The choice of stainless steel ensures durability, resistance to corrosion, and ease of sterilization, all of which are critical for maintaining a sterile and contaminant-free environment during the drug manufacturing process. The conical shape offers several advantages, including better mixing and efficient sedimentation of cells or particles, which is essential for optimizing the production process.
The perfusion system integrated into this bioreactor is a game-changer. It allows for a continuous supply of fresh nutrients and the removal of waste products, creating an environment that closely mimics the physiological conditions within the body. This leads to enhanced cell growth, viability, and productivity, ultimately resulting in higher yields of the desired therapeutic compounds.
One of the key benefits of this bioreactor system in pharma manufacturing is its ability to produce large quantities of high-quality drugs. In an industry where the demand for effective and safe medications is constantly growing, the scalability and reproducibility offered by the 200 Liter Conical Stainless Fermenter are of paramount importance. It enables pharmaceutical companies to meet the market demands consistently while adhering to strict quality control standards.
The controlled environment within the bioreactor is precisely regulated to maintain optimal conditions for cell culture and drug synthesis. Parameters such as temperature, pH, dissolved oxygen levels, and shear stress are meticulously monitored and adjusted in real-time. This level of control ensures that the cells are functioning at their peak performance, maximizing the output of the desired therapeutic molecules.
In addition to traditional small molecule drugs, bioreactors play a vital role in the production of biologics, such as monoclonal antibodies and recombinant proteins. These complex molecules often require specific culture conditions and the gentle handling provided by the perfusion system to maintain their structural integrity and biological activity. The ability to precisely control the bioreactor environment is essential for ensuring the quality and efficacy of these therapeutics.
The 200 Liter Stainless Conical Fermenter also contributes to the development of personalized medicine. With the increasing focus on tailoring treatments to individual patients' genetic and physiological profiles, bioreactors can be used to produce small batches of customized drugs. This flexibility allows for more targeted and effective therapies, improving patient outcomes and addressing the unique needs of different patient populations.
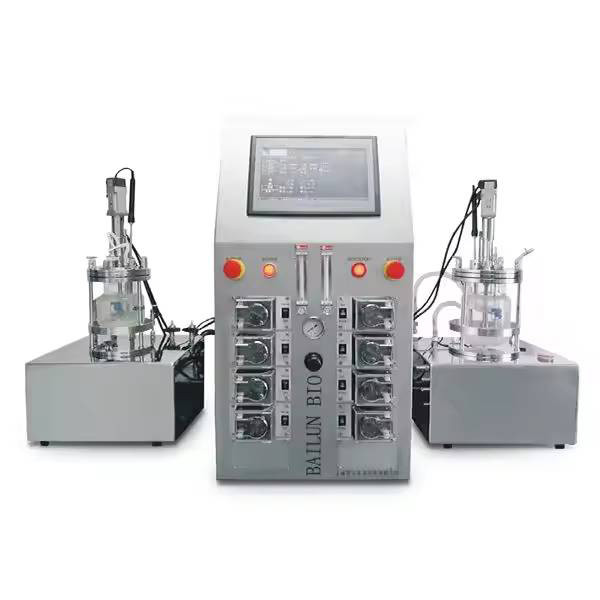
However, the operation and maintenance of such advanced bioreactor systems come with their own set of challenges. The complexity of the equipment requires highly trained and skilled operators who understand the intricacies of the process control and troubleshooting. Regular calibration and validation of sensors and control systems are necessary to ensure the accuracy and reliability of the data and operations.
Furthermore, the cleaning and sterilization procedures for the bioreactor are critical to prevent cross-contamination between different batches and to maintain product purity. The use of appropriate cleaning agents and validation of the sterilization process are essential steps in ensuring the integrity and safety of the drugs produced.
Despite these challenges, the benefits of the Pharma Manufacturing Bioreactor with a perfusion system far outweigh the difficulties. The continuous advancements in bioreactor technology are driving down the cost of production, reducing the time to market for new drugs, and improving the overall competitiveness of the pharmaceutical industry.
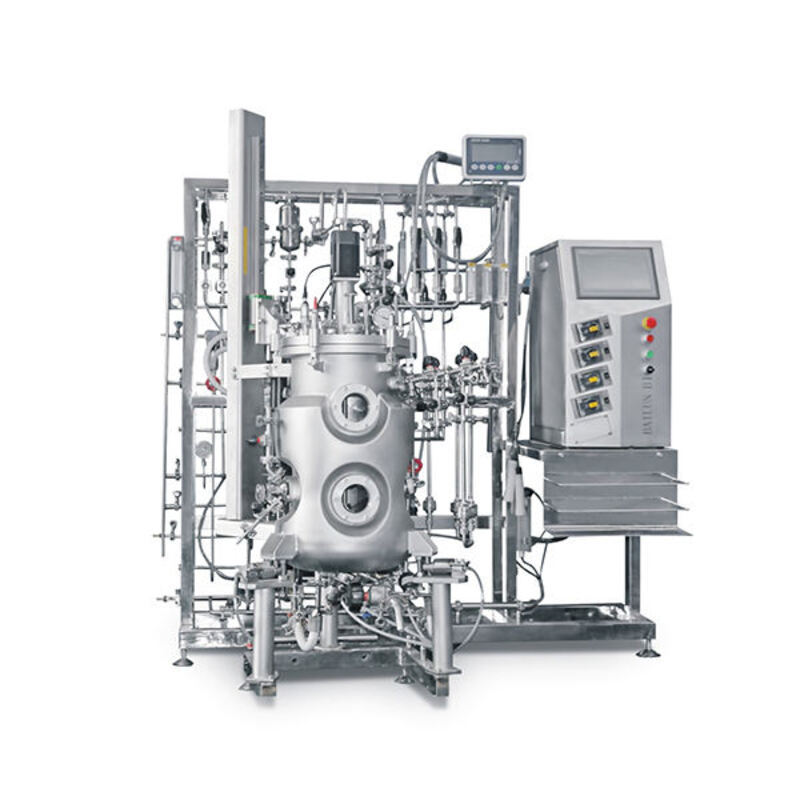
Looking ahead, the future of pharma manufacturing bioreactors looks promising. Research and development efforts are focused on further improving the efficiency and functionality of these systems. This includes the development of more advanced sensors for real-time monitoring of intracellular processes, the integration of artificial intelligence and machine learning for predictive process control, and the exploration of novel materials and designs to enhance bioreactor performance.
In conclusion, the Liter Stainless Conical 200 Fermenter with a perfusion system is a cornerstone of modern pharmaceutical manufacturing. It represents the convergence of engineering excellence and biological science, enabling the production of life-saving drugs with greater efficiency, quality, and innovation. As the industry continues to evolve and embrace new technologies, these bioreactors will undoubtedly play an even more significant role in shaping the future of healthcare and improving the lives of patients worldwide.