The 2000L Bioreactor: A Catalyst for Innovation and Production
- Share
- Issue Time
- Jul 25,2024
Summary
The 2000L Bioreactor: A Catalyst for Innovation and Production
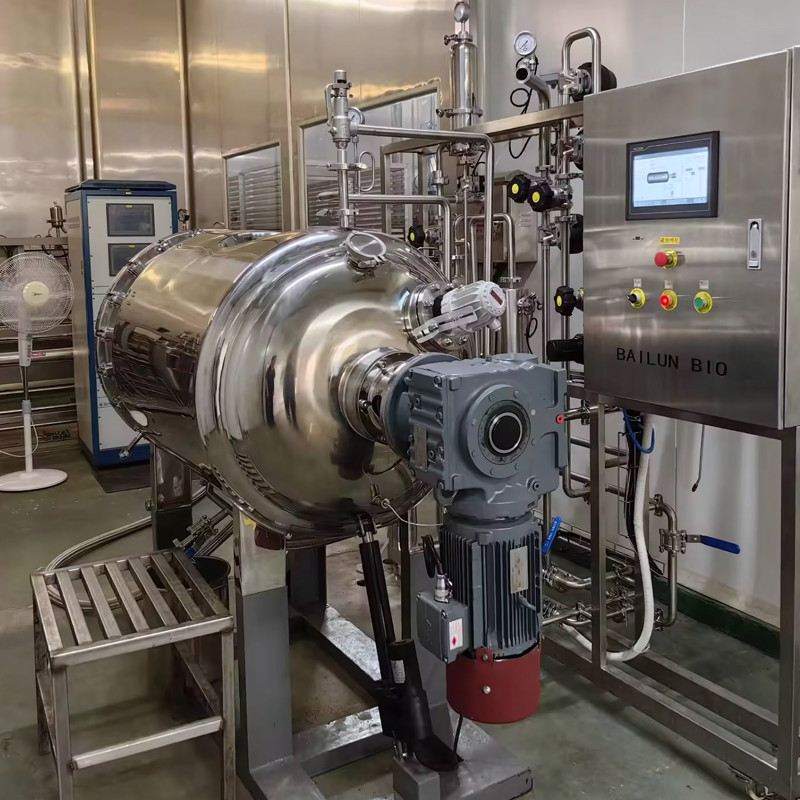
In the landscape of modern biotechnology and industrial processes, the 2000L bioreactor has emerged as a critical component, driving advancements and shaping the future of various sectors. This article aims to provide a comprehensive exploration of the 2000L bioreactor, covering its design, functionality, applications, and the impact it has on diverse industries.
The design of a 2000L bioreactor is a meticulous process that combines engineering precision with biological requirements. The vessel itself is typically constructed from materials that offer durability, chemical resistance, and the ability to withstand sterilization processes. Stainless steel is often the material of choice due to its excellent properties in these aspects.
The internal configuration of the bioreactor is designed to optimize the growth and productivity of the biological entities within. Agitation systems, such as impellers or magnetic stirrers, are strategically placed to ensure uniform mixing of the contents. This is crucial for the homogeneous distribution of nutrients, oxygen, and heat, creating a consistent environment throughout the 2000L volume.
Temperature control is a vital aspect of the design. Jackets or coils surrounding the vessel allow for the circulation of heating or cooling fluids, enabling precise maintenance of the optimal temperature range. Different organisms and processes have specific temperature requirements, and the ability to accurately regulate temperature is essential for successful cultivation and product formation.
Oxygen supply is another key consideration. Aeration systems, including spargers or membrane oxygenators, are incorporated to provide the necessary oxygen for aerobic processes. The rate of oxygen transfer is carefully calibrated to meet the metabolic demands of the organisms without causing excessive foaming or oxygen stress.
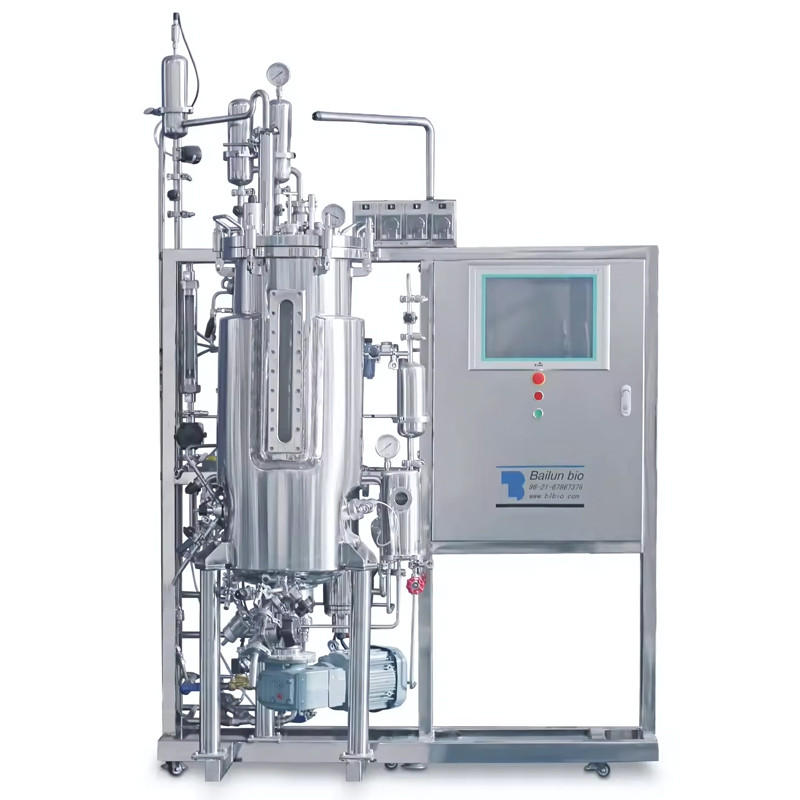
The functionality of the 2000L bioreactor lies in its ability to provide a controlled and scalable environment for a wide range of biological processes. It allows for precise monitoring and adjustment of parameters such as pH, dissolved oxygen levels, and nutrient concentrations. Sophisticated sensors and control systems ensure that the conditions within the bioreactor remain within the desired range, promoting efficient growth and metabolic activities.
One of the significant applications of the 2000L bioreactor is in the production of pharmaceuticals. It is used for the cultivation of microbial or mammalian cells to produce therapeutic proteins, antibodies, and vaccines. The controlled environment and scalability of the bioreactor make it possible to generate large quantities of these life-saving drugs with consistent quality and purity.
In the field of biotechnology research, the 2000L bioreactor Cell Culture serves as a valuable tool for studying the behavior and metabolism of cells and microorganisms. It enables researchers to optimize culture conditions, investigate genetic modifications, and develop new bioprocesses. This knowledge gained from laboratory-scale experiments can then be translated to larger-scale production using similar bioreactor systems.
The food and beverage industry also benefits from the 2000L bioreactor. It is employed in the production of enzymes, flavors, and probiotics. The controlled fermentation processes within the bioreactor ensure the quality and consistency of these products, meeting the demands of consumers for high-quality and safe food and beverages.
Environmental applications include the treatment of wastewater and the production of biofuels. Microorganisms in the 2000L bioreactor can break down contaminants in wastewater, reducing its environmental impact. Additionally, it can be used for the cultivation of algae or other organisms for the synthesis of biofuels, contributing to sustainable energy solutions.
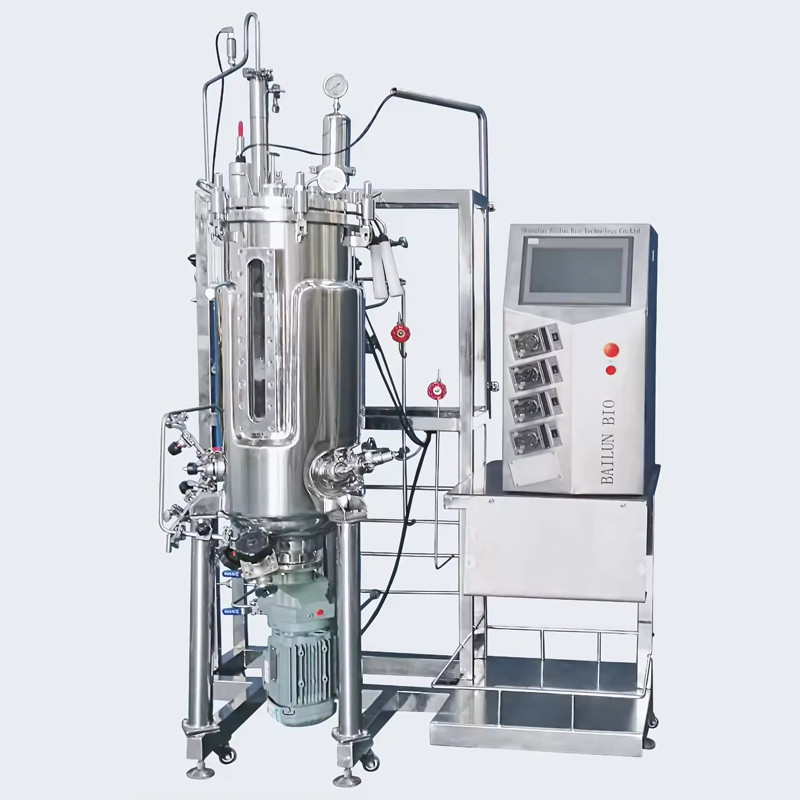
However, operating a 2000L bioreactor comes with its challenges. Maintaining sterility is of utmost importance to prevent contamination, which can lead to batch failure and significant economic losses. Regular cleaning and sterilization procedures, along with strict adherence to good manufacturing practices, are essential.
Scaling up from smaller laboratory-scale bioreactors to the 2000L size requires careful consideration of various factors. Changes in fluid dynamics, mass transfer, and heat transfer can affect the performance of the process. Therefore, extensive validation and optimization studies are necessary to ensure that the larger-scale operation replicates the success achieved at the smaller scale.
Despite these challenges, the 2000L bioreactor remains an indispensable asset in the pursuit of scientific and industrial progress. Ongoing research and development efforts are focused on improving its design, functionality, and control systems to meet the ever-growing demands of different industries.
In conclusion, the 2000L bioreactor is not just a piece of equipment; it is a catalyst for innovation and production across multiple fields. Its ability to provide a controlled and scalable environment for biological processes makes it a vital component in the drive towards a more sustainable, healthy, and scientifically advanced future.