The Crucial Role of Bioreactors and Fermenters in Industrial Cultures
- Share
- Issue Time
- Jul 2,2024
Summary
The Crucial Role of Bioreactors and Fermenters in Industrial Cultures
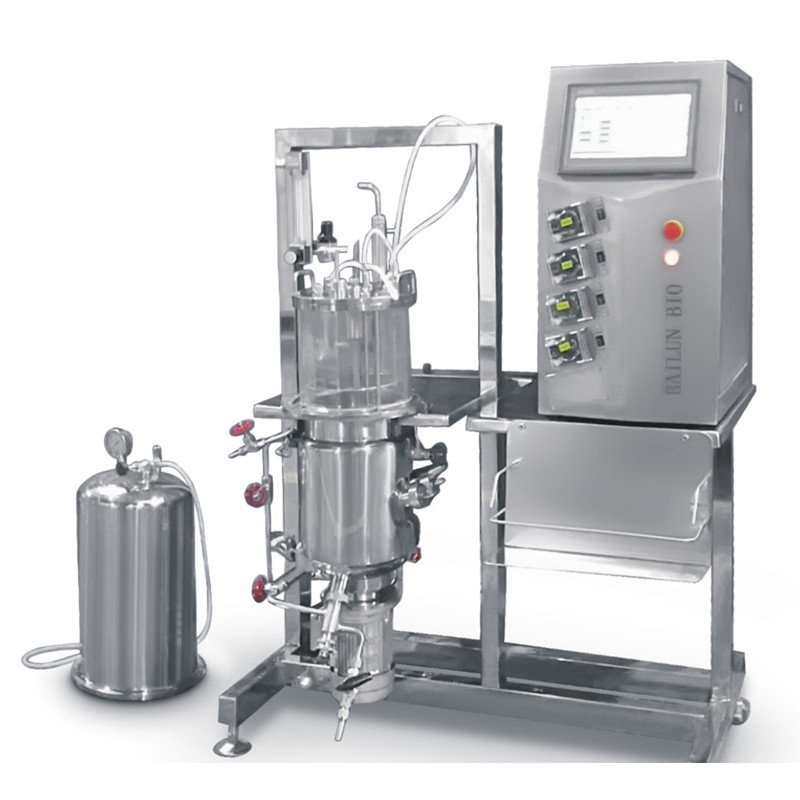
In the modern industrial landscape, the significance of advanced equipment such as bioreactors and fermenters cannot be overstated. These technological marvels have revolutionized various industries, enabling efficient and large-scale production of a wide range of valuable products.
Bioreactors and fermenters are at the heart of industrial cultures, providing controlled environments for biological processes to occur. They play a vital role in the production of pharmaceuticals, food and beverages, biofuels, and numerous other essential commodities.
The design and functionality of bioreactors are highly sophisticated. They are engineered to maintain precise conditions that are optimal for the growth and metabolism of the organisms or cells involved. Temperature, pH, dissolved oxygen levels, nutrient supply, and agitation are just some of the parameters that can be precisely regulated within these vessels.
For instance, in the pharmaceutical industry, bioreactors are used for the production of therapeutic proteins, antibodies, and vaccines. The ability to control the environment within the bioreactor ensures that the cells expressing these valuable biomolecules grow and function properly, resulting in high-quality and consistent products. The precise control over parameters like pH and dissolved oxygen helps maintain the stability and activity of the enzymes and pathways involved in the production process.
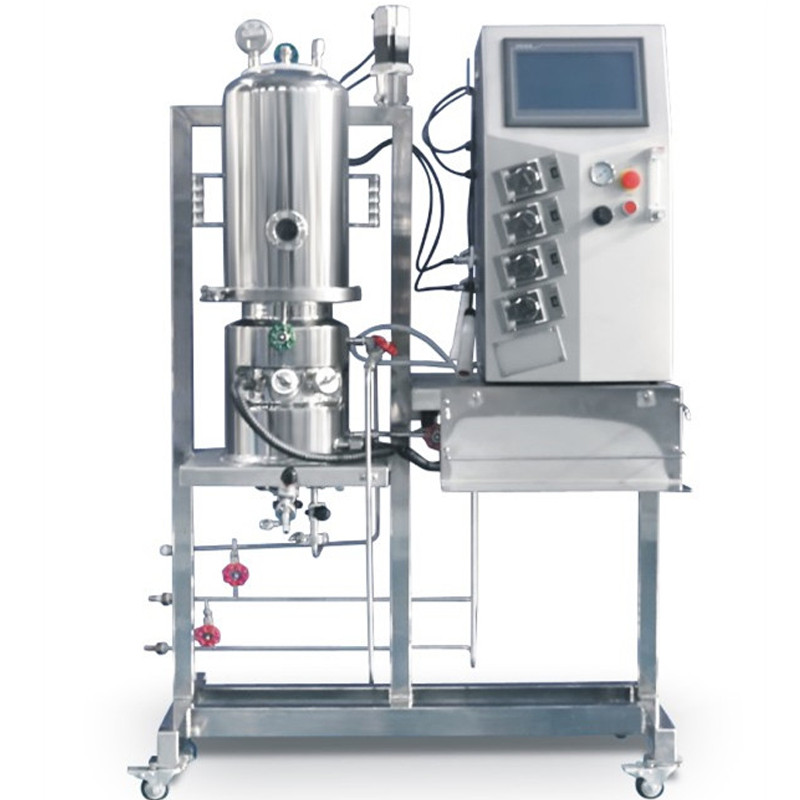
Fermenters, on the other hand, are commonly employed in the food and beverage sector. They are essential for the production of alcoholic beverages like beer and wine, as well as for the fermentation of dairy products and the creation of various food additives and enzymes. In these applications, the fermenter provides the right conditions for the microorganisms to carry out the desired biochemical conversions, resulting in the characteristic flavors, textures, and properties of the final products.
In the biofuel industry, bioreactors and fermenters are critical for the conversion of biomass into sustainable energy sources. Microorganisms or enzymes within these systems break down complex organic matter to produce bioethanol, biodiesel, or other biofuels. The efficient operation of these reactors is crucial for maximizing the yield and reducing the costs associated with biofuel production, making them more competitive with traditional fossil fuels.
One of the key advantages of using bioreactors and fermenters in industrial cultures is the scalability. These systems can be designed and operated at different scales, from small pilot plants for research and development to large industrial-scale facilities capable of meeting the high demand for products. The scalability allows companies to start with small-scale experiments to optimize the process and then scale up smoothly to commercial production, minimizing risks and maximizing returns on investment.
However, operating these complex systems comes with its own set of challenges. Maintaining aseptic conditions is of paramount importance to prevent contamination, which can lead to product spoilage and significant economic losses. The monitoring and control systems must be highly reliable and accurate to ensure that the process parameters remain within the desired range at all times. Any deviations can have a detrimental effect on the quality and quantity of the final product.
The selection of the appropriate type of bioreactor or fermenter for a specific application is also a crucial decision. Different processes require different designs and features. For example, a stirred-tank bioreactor might be suitable for some applications where thorough mixing is necessary, while a bubble column bioreactor might be more appropriate for processes that require gentle aeration.
The materials used in the construction of these reactors also need to be carefully chosen. They must be resistant to corrosion, compatible with the process fluids, and able to withstand the mechanical stresses and temperature variations associated with the operation. Additionally, the cost of the equipment, including installation, operation, and maintenance, is an important consideration, especially for large-scale industrial operations.
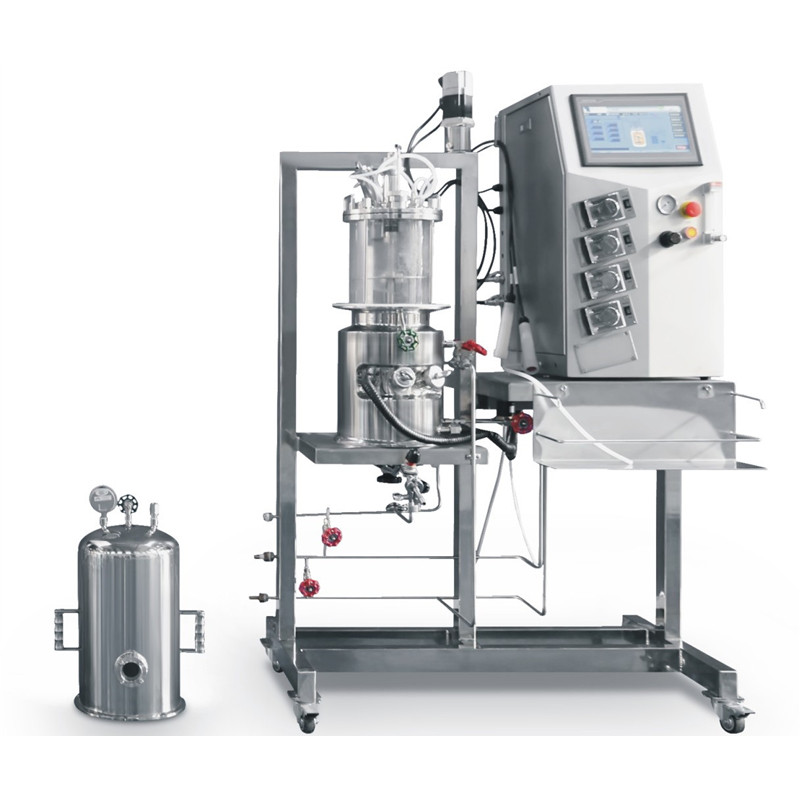
Advancements in technology are constantly improving the performance and capabilities of bioreactors and fermenters. The integration of sensors, data analytics, and artificial intelligence is enabling real-time monitoring and predictive control, allowing for more efficient and optimized operation. New materials and coatings are enhancing the biocompatibility and durability of the reactors.
In conclusion, bioreactors and fermenters are indispensable tools in modern industrial cultures. Their ability to provide controlled and scalable environments for biological processes has transformed the way we produce a wide range of essential products. Continued research and development in this field will further enhance their efficiency, reliability, and sustainability, driving innovation and growth in various industries and contributing to a more prosperous and sustainable future.