bioreactors play a crucial role in facilitating various biological processes for the production of valuable substances
- Share
- Issue Time
- Jul 2,2024
Summary
bioreactors play a crucial role in facilitating various biological processes for the production of valuable substances
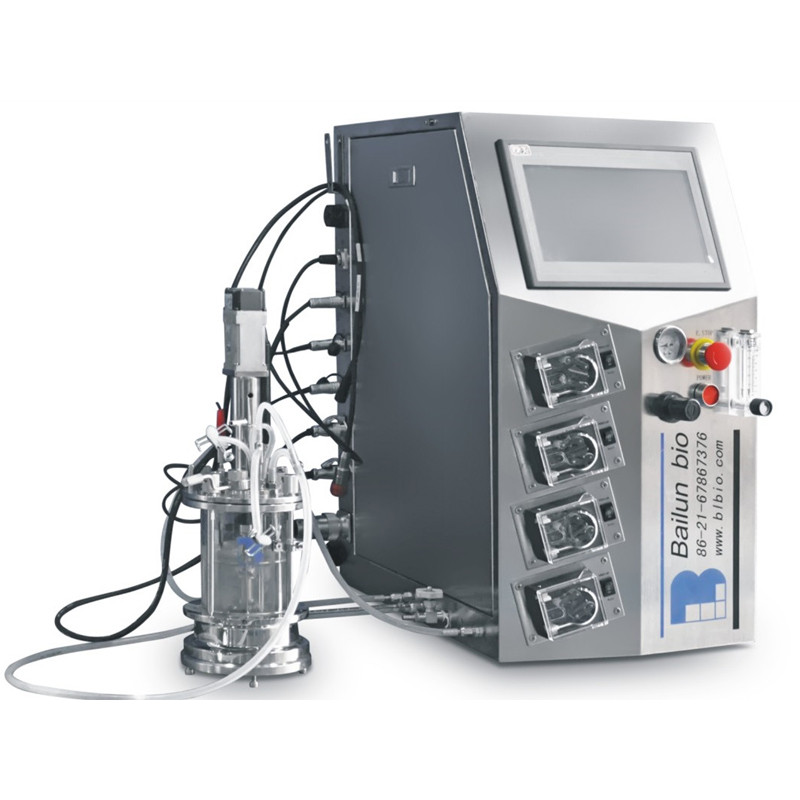
In the field of biotechnology and biochemical engineering, bioreactors play a crucial role in facilitating various biological processes for the production of valuable substances. Among the different types of bioreactors, Stirred Tank Bioreactors, Mini Bioreactors, Fermenters, and Multistage Bioreactors each have unique characteristics and applications that contribute to the advancement of scientific research and industrial production.
The Stirred Tank Bioreactor is one of the most commonly used designs in large-scale industrial operations. It consists of a cylindrical vessel with a mechanical agitator to ensure uniform mixing of the contents. This type of bioreactor offers several advantages, such as excellent mass transfer and heat transfer capabilities, which are essential for maintaining optimal conditions for cell growth and metabolite production.
The agitation system in a Stirred Tank Bioreactor helps distribute nutrients, oxygen, and other essential components evenly throughout the reactor volume. This homogeneity is critical for preventing the formation of gradients that could adversely affect the performance and productivity of the biological system. Moreover, the ability to control the speed and type of agitation allows for customization based on the specific requirements of the process and the characteristics of the organisms being cultivated.
For example, in the production of antibiotics using microbial fermentation, a Stirred Tank Bioreactor can be precisely configured to provide the right amount of agitation to ensure that the microorganisms have access to sufficient nutrients and oxygen, while also avoiding excessive shear stress that could damage the cells. The controlled mixing also helps in maintaining a consistent pH and temperature, which are crucial factors for the efficient synthesis of the desired antibiotic.
Mini Bioreactors, on the other hand, have gained popularity in recent years, especially in the realm of research and development. These compact systems offer several benefits for early-stage experimentation and process optimization. Their smaller size makes them more manageable in terms of resource requirements, space, and cost.
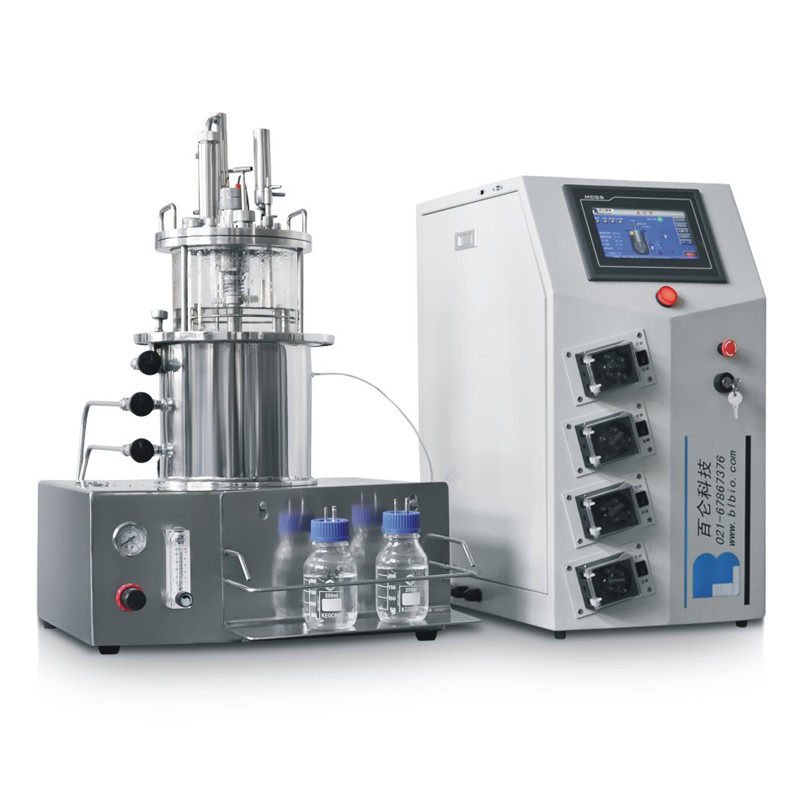
Mini Bioreactors are often used in academic and research laboratories to conduct preliminary studies on new cell lines, culture conditions, and metabolic pathways. They allow researchers to quickly test hypotheses and gather valuable data on a smaller scale before scaling up to larger production systems. The portability and ease of operation of these miniaturized bioreactors also facilitate parallel experiments, enabling the comparison of multiple conditions simultaneously.
For instance, in the field of synthetic biology, where the goal is to engineer microorganisms to produce novel compounds, Mini Bioreactors can be employed to assess the performance of different genetic constructs and metabolic engineering strategies. The rapid feedback and reduced sample volume requirements make it possible to iterate through different designs more efficiently, accelerating the discovery and development process.
The Fermenter is another important type of bioreactor that is widely utilized in various industries. Fermenters can be classified based on the nature of the organisms being cultivated (e.g., aerobic or anaerobic) and the mode of operation (batch, fed-batch, or continuous). Aerobic fermenters are equipped with systems to supply adequate oxygen, while anaerobic fermenters are designed to maintain an oxygen-free environment.
In the food and beverage industry, fermenters are essential for the production of alcoholic beverages, dairy products, and fermented foods. For example, in the brewing of beer, a specific type of fermenter is used to control the fermentation process of yeast, resulting in the formation of alcohol and the development of flavor and aroma compounds. In the dairy sector, fermenters are employed for the production of yogurt and cheese, where lactic acid bacteria play a crucial role in transforming milk into the final products.
Multistage Bioreactors represent a more complex and advanced configuration that offers enhanced process control and increased productivity. These systems consist of multiple compartments or stages, each with its own set of controlled conditions. This design allows for the sequential occurrence of different reactions or processes within a single bioreactor, reducing the need for multiple separate units and streamlining the overall production process.
For example, in a multistage bioreactor used for the production of complex biopharmaceuticals, the first stage might be optimized for cell growth, while the subsequent stages could be tailored for product synthesis and purification. The ability to precisely control the conditions at each stage enables better management of the entire process and can lead to higher yields and improved product quality.
One of the challenges associated with the use of different bioreactor types is the scalability. Moving from small-scale experiments conducted in Mini Bioreactors or laboratory-scale fermenters to large-scale industrial Stirred Tank Bioreactors or Multistage Bioreactors requires careful consideration of various factors, such as fluid dynamics, mass transfer rates, and heat transfer coefficients. Mathematical modeling and pilot-scale studies are often employed to predict and optimize the performance of the process at the larger scale.
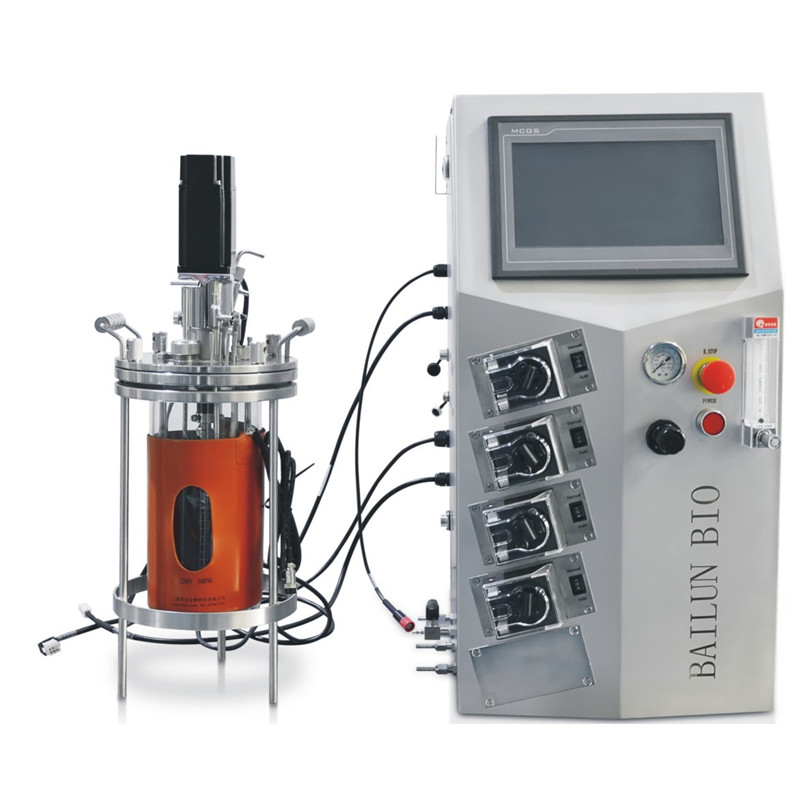
Another important aspect is the monitoring and control of the bioreactor systems. Advanced sensors and control algorithms are constantly being developed to provide real-time data on key parameters such as cell density, metabolite concentrations, pH, and dissolved oxygen. This information is crucial for making timely adjustments to the process conditions to ensure optimal performance and product quality.
In conclusion, the diverse range of bioreactor systems, including Stirred Tank Bioreactors, Mini Bioreactors, Fermenters, and Multistage Bioreactors, provides scientists and engineers with powerful tools to address the complex challenges of modern biotechnology and biochemical engineering.
The selection of the appropriate bioreactor type depends on factors such as the scale of production, the nature of the process, and the specific requirements of the organisms and products involved. Continued innovation and improvement in bioreactor design and operation will undoubtedly contribute to the development of more efficient and sustainable bioprocesses, driving progress in fields such as healthcare, agriculture, and environmental remediation.