Insights into the Automatic Fermenter Bioreactor (100L) for Bacteria
- Share
- Issue Time
- Jul 20,2024
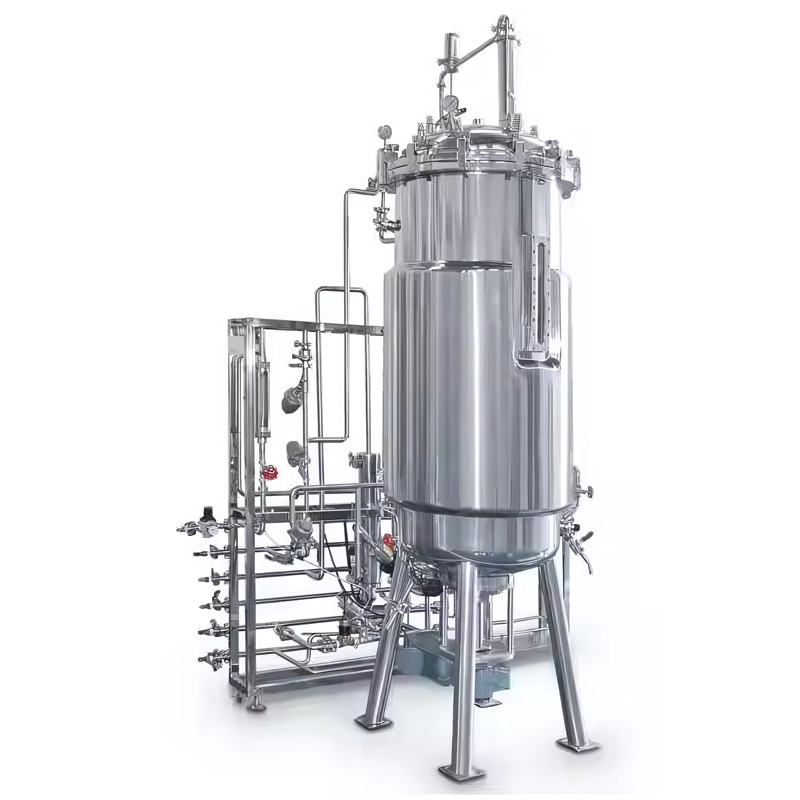
Question 1: What are the key features of an Automatic Fermenter Bioreactor (100L)?
An Automatic Fermenter Bioreactor (100L) typically comes with advanced control systems for precise regulation of parameters such as temperature, pH, dissolved oxygen, and agitation speed. It is designed with a large capacity to handle significant volumes of culture, while also ensuring uniform conditions throughout the vessel.
Question 2: How does the automatic control system benefit the bacterial fermentation process?
The automatic control system allows for real-time monitoring and immediate adjustments of critical parameters. This helps maintain an optimal environment for bacterial growth and metabolism, reducing variations and increasing the consistency and quality of the final product.
Question 3: Can this 100L fermenter be used for different types of bacteria?
Yes, but the specific configuration and parameters may need to be adjusted based on the unique requirements of each bacterial species. Factors such as growth rate, oxygen demand, and nutrient preferences need to be considered.
Question 4: What kind of maintenance is required for the 100L Automatic Fermenter Bioreactor?
Regular maintenance includes cleaning and sterilization of the vessel and its components to prevent contamination. Checking and calibrating sensors, as well as inspecting mechanical parts like agitators and pumps, are also essential.
Question 5: How is the sterilization process carried out in this fermenter?
Common methods include steam sterilization or the use of chemical sterilants. The specific sterilization protocol depends on the design of the fermenter and the nature of the bacteria being cultivated.
Question 6: What safety measures should be taken when operating this type of fermenter?
Operators should follow strict safety protocols, including wearing appropriate protective equipment, ensuring proper ventilation, and being trained in handling potential emergencies such as pressure build-up or leaks.
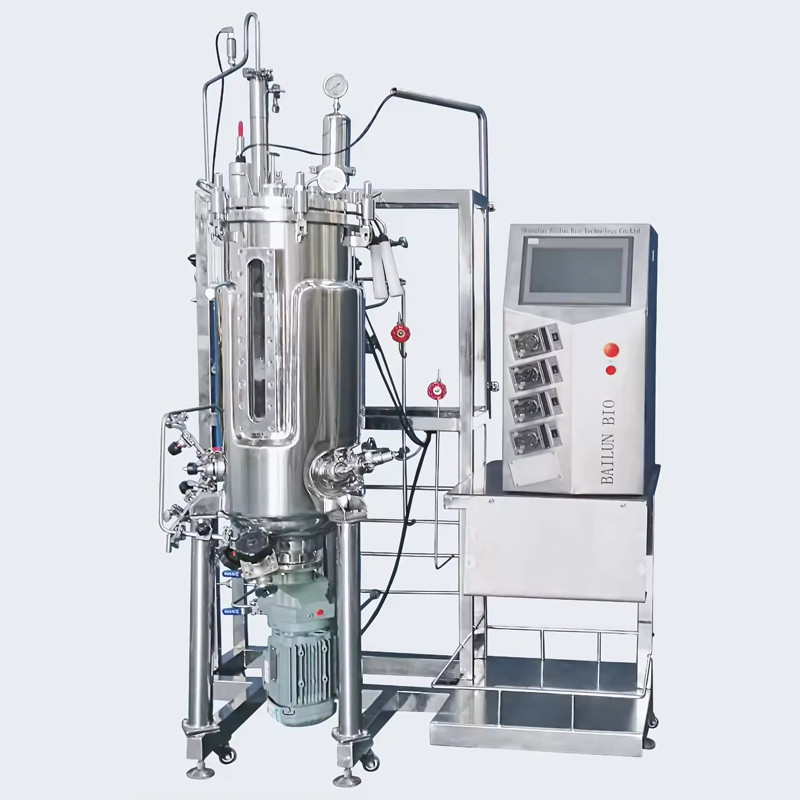
Question 7: How can one optimize the performance of the 100L Automatic Fermenter Bioreactor for specific bacterial cultures?
This can be achieved by conducting preliminary experiments to determine the ideal parameters for the particular bacteria. Fine-tuning factors like inoculum size, nutrient composition, and aeration rates can significantly enhance the productivity.
Question 8: Can the data collected from the fermenter be used for process improvement and analysis?
Yes, the data on parameters like temperature, pH, and cell growth can be analyzed to identify trends, optimize the process, and troubleshoot any issues that arise during fermentation.
Question 9: What are the common challenges faced when using an Automatic Fermenter Bioreactor and how can they be addressed?
Challenges can include maintaining sterility, dealing with foaming, and optimizing oxygen transfer. Addressing these often involves proper equipment setup, using antifoaming agents, and adjusting the aeration and agitation systems.
Question 10: Is it possible to scale up the process from the 100L fermenter to larger industrial-scale systems?
Yes, but careful consideration of factors such as fluid dynamics, heat transfer, and mass transfer is necessary during the scale-up process to ensure comparable performance and product quality.
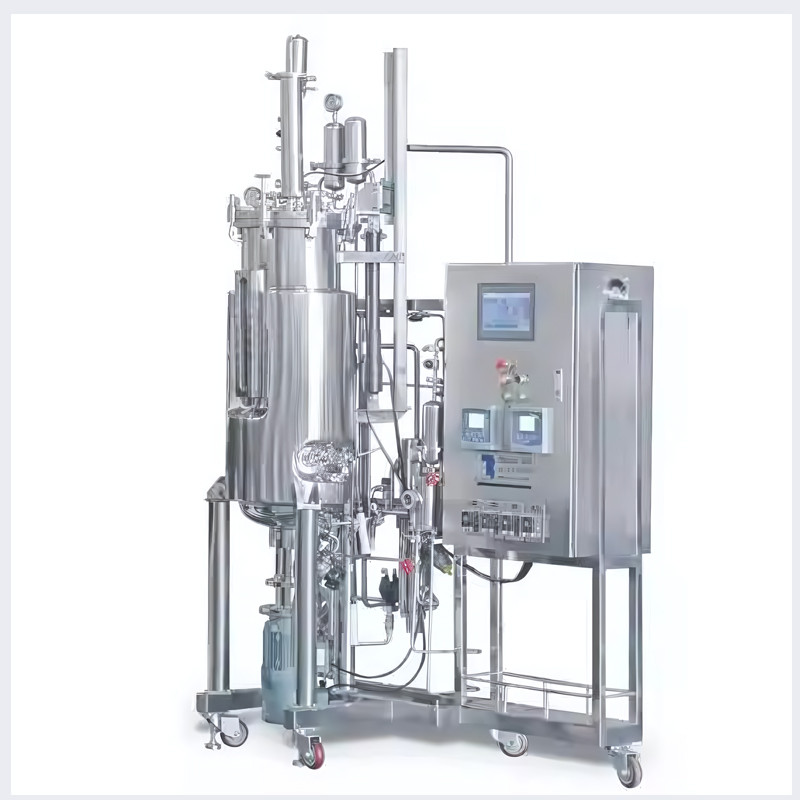