Driving Advancements in Industrial Fermentation and Plant Cell Cultivation
- Share
- Issue Time
- Jun 26,2024
Summary
Stainless Steel Fermenter Bioreactor: Driving Advancements in Industrial Fermentation and Plant Cell Cultivation
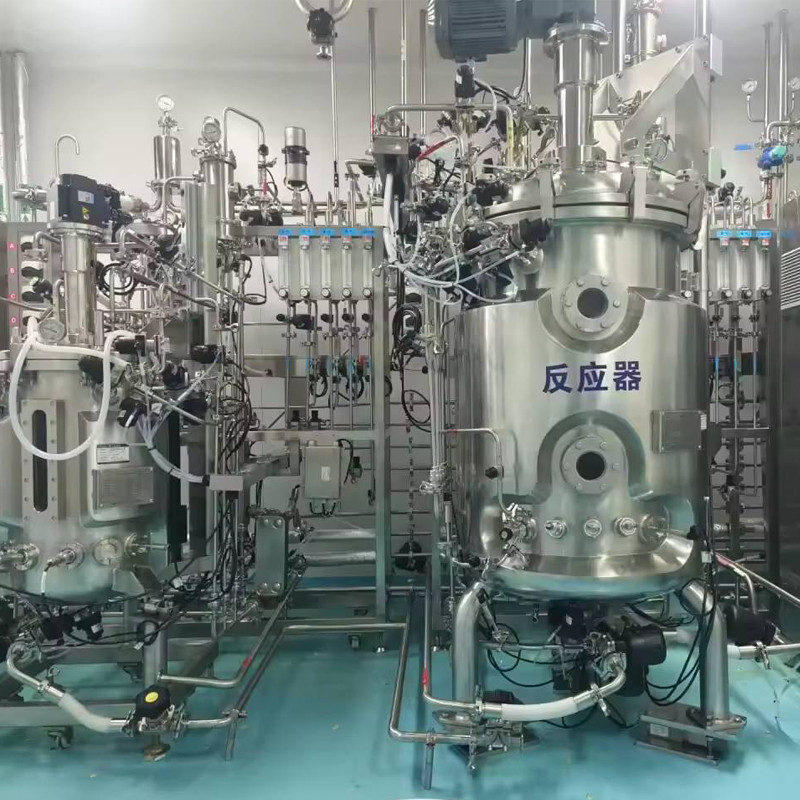
In the dynamic landscape of modern biotechnology and industrial processes, the Stainless Steel Fermenter Bioreactor has emerged as a linchpin, facilitating efficient and controlled production in various domains. This article delves into the significance, features, applications, and future prospects of the Stainless Steel Fermenter Bioreactor, with a particular focus on its role in industrial fermentation and plant cell cultivation.
The Stainless Steel Fermenter Bioreactor is a testament to engineering excellence. Crafted from stainless steel, it offers several distinct advantages. Stainless steel is renowned for its durability, resistance to corrosion, and ability to withstand high temperatures and pressures. This makes the bioreactor suitable for long-term and rigorous use in industrial settings. The inert nature of stainless steel also minimizes the risk of chemical reactions with the contents of the reactor, ensuring the purity and integrity of the fermentation process.
One of the key features of this bioreactor is its precise control systems. In industrial fermentation, maintaining optimal conditions for microbial growth and metabolite production is crucial. The Stainless Steel Fermenter Bioreactor is equipped with sensors and controllers that monitor and regulate parameters such as temperature, pH, dissolved oxygen, and agitation speed. This level of control allows for consistent and reproducible results, which is essential for large-scale production and quality control.
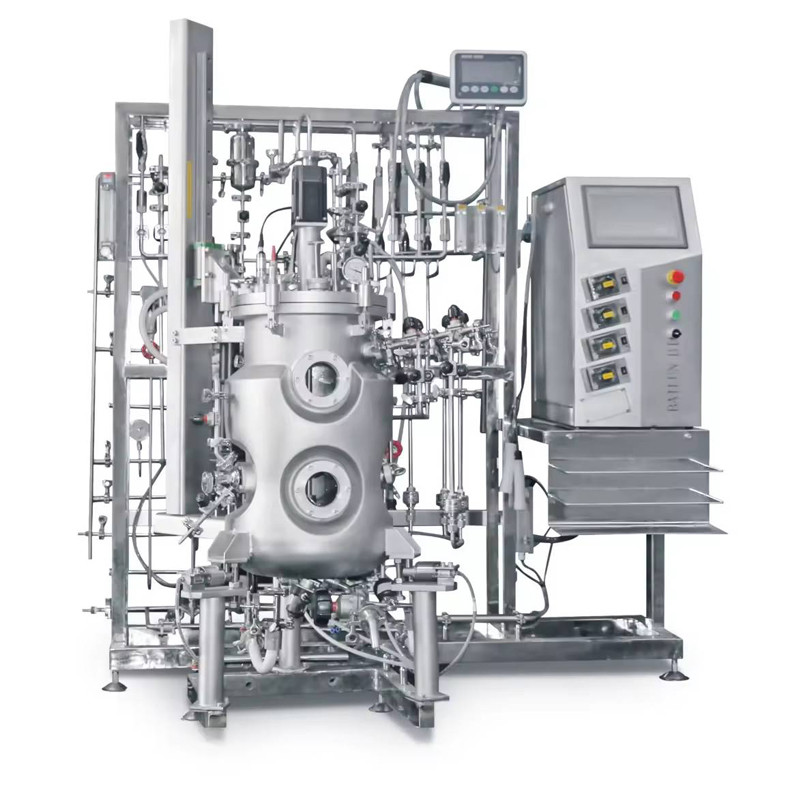
For example, in the production of antibiotics or enzymes, maintaining a specific temperature range can significantly impact the yield and activity of the desired product. The ability to precisely adjust and maintain the pH is also vital as it affects the enzymatic processes within the microorganisms. The dissolved oxygen concentration is another critical factor that influences the metabolic pathways and growth rate of the microbes. The agitation speed ensures uniform distribution of nutrients and oxygen throughout the reactor, preventing the formation of gradients that could lead to uneven growth and product formation.
In the context of plant cell cultivation, the Stainless Steel Fermenter Bioreactor presents unique opportunities and challenges. Plant cells have different growth requirements compared to microbial cells, and the bioreactor needs to be tailored accordingly. Specialized culture media, growth regulators, and aeration systems are often employed to support the growth and differentiation of plant cells.
Plant cell cultivation in bioreactors has gained significant attention in recent years due to its potential for the production of valuable secondary metabolites, such as pharmaceuticals and natural compounds. The controlled environment provided by the Stainless Steel Fermenter Bioreactor enables researchers to manipulate the growth conditions and metabolic pathways of plant cells to enhance the production of these compounds. Additionally, it offers a scalable solution for large-scale production, reducing the reliance on traditional methods such as extraction from wild plants, which may be environmentally unsustainable and limited in supply.
The industrial applications of the Stainless Steel Fermenter Bioreactor are vast and diverse. In the food and beverage industry, it is used for the production of beverages like beer and wine, as well as for the fermentation of dairy products and the manufacture of food additives. The bioreactor's ability to control the fermentation process ensures consistent quality, flavor, and texture of the final products.
In the pharmaceutical sector, it plays a crucial role in the production of biopharmaceuticals, including monoclonal antibodies and vaccines. The high level of control and sterility provided by the stainless steel construction is essential to meet the strict regulatory requirements of the healthcare industry.

The bioreactor is also indispensable in the field of biofuels. Microbial fermentation in the Stainless Steel Fermenter Bioreactor can convert biomass into ethanol or other biofuels, contributing to the development of sustainable energy solutions.
However, operating and maintaining a Stainless Steel Fermenter Bioreactor requires significant expertise and attention to detail. Regular sterilization is necessary to prevent contamination and ensure the purity of the culture. This often involves complex procedures such as steam sterilization or the use of chemical disinfectants. The monitoring and calibration of sensors and control systems are crucial to ensure accurate and reliable operation. Any malfunction or deviation in the controlled parameters can have significant implications for the productivity and quality of the fermentation process.
Looking towards the future, the Stainless Steel Fermenter Bioreactor is expected to undergo further advancements and innovations. The integration of advanced technologies such as artificial intelligence and machine learning will enable more intelligent control and optimization of the fermentation process. Real-time monitoring and data analytics will allow for predictive maintenance and early detection of potential issues. Additionally, research is ongoing to develop more efficient and sustainable bioreactor designs, including improvements in energy consumption and waste management.
In conclusion, the Stainless Steel Fermenter Bioreactor stands as a vital component of modern industrial biotechnology. Its role in industrial fermentation and plant cell cultivation is indispensable, driving innovation and enabling the production of a wide range of valuable products. As technology continues to evolve, this bioreactor is set to play an even more significant role in shaping the future of sustainable and efficient bioprocessing.