Key parameter in bioreactor cell culture: dissolved oxygen (DO value)
- Share
- Issue Time
- Jan 10,2025
Summary
In the process of biological reaction production, DO value is generally used as the parameter for dissolved oxygen, and DO value is one of the most critical parameters in the entire fermentation process

In the biological reaction production process, DO value is generally used as the parameter for dissolved oxygen, and DO value is one of the most critical parameters in the entire fermentation process.
It can intuitively reflect the dynamic changes in the entire fermentation process, and indirectly reduce fermentation production time and energy consumption by increasing the DO value, thereby improving the yield and quality of the final product.
Dissolved oxygen is one of the most important parameters for controlling aerobic fermentation. Due to the low solubility of oxygen in water and fermentation broth, it is necessary to continuously adjust ventilation and stirring to meet the oxygen requirements of different fermentation processes.
The size of dissolved oxygen has different effects on bacterial growth, product formation, and yield.
Here, we will introduce the changes in dissolved oxygen concentration at different times, the reasons for abnormal decreases/increases in dissolved oxygen, and the aspects of oxygen supply and consumption.
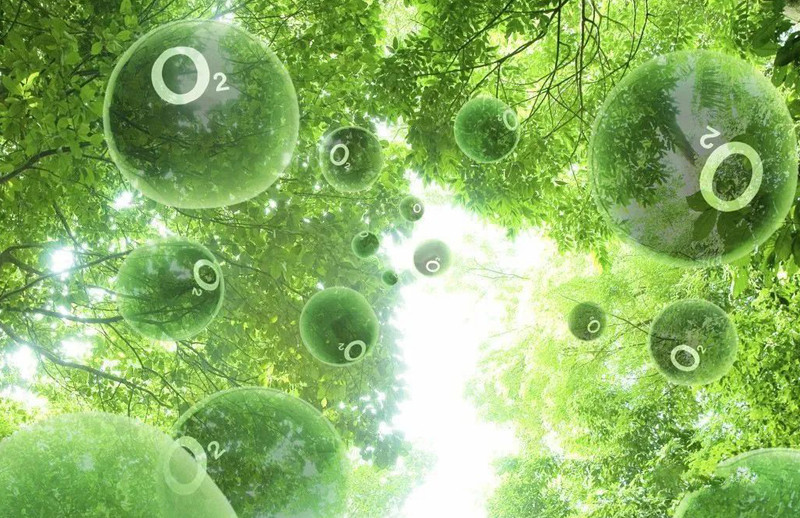
The change in dissolved oxygen concentration during fermentation follows its own pattern for each product under certain fermentation conditions. Usually, the change in dissolved oxygen concentration is divided into three stages.
During the logarithmic growth phase, the DO value decreases significantly, and the rate of decrease can roughly estimate the growth status of the bacteria;
At the end of the logarithmic growth period, there will be a low point of dissolved oxygen; In the later stage of fermentation, due to the aging of the bacterial cells, the respiratory intensity decreases and the dissolved oxygen concentration gradually increases.
Once the bacterial cells self dissolve, the increase in dissolved oxygen concentration will be more significant.
The reason for the abnormal decrease/increase in dissolved oxygen is that during the fermentation process, there may be abnormal changes in dissolved oxygen concentration, such as a significant decrease or increase.
There are many reasons for this, but fundamentally it is caused by the imbalance of oxygen supply and demand due to changes in oxygen consumption or supply.
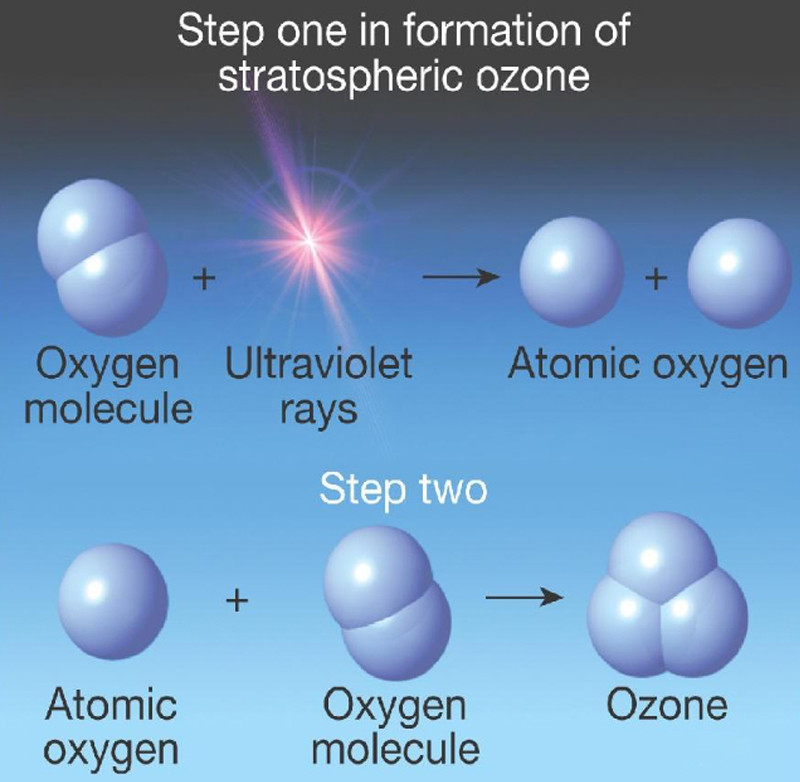
The abnormal decrease in dissolved oxygen during fermentation may be due to the following reasons:
① Polluting aerobic bacteria, a large amount of dissolved oxygen is consumed, causing dissolved oxygen to drop to near zero in a short period of time
② Abnormal metabolism of bacterial cells leads to an increase in oxygen demand, resulting in a decrease in dissolved oxygen
③ Equipment or process control that affects oxygen supply malfunctions or changes, causing a decrease in dissolved oxygen.
If the stirring power consumption decreases or the stirring rate slows down, it will affect the oxygen supply capacity and reduce the dissolved oxygen
The main reason for the abnormal increase in dissolved oxygen is the significant decrease in oxygen consumption. If highly reactive bacteriophages are contaminated, the respiration of the producing bacteria is inhibited, and dissolved oxygen increases.
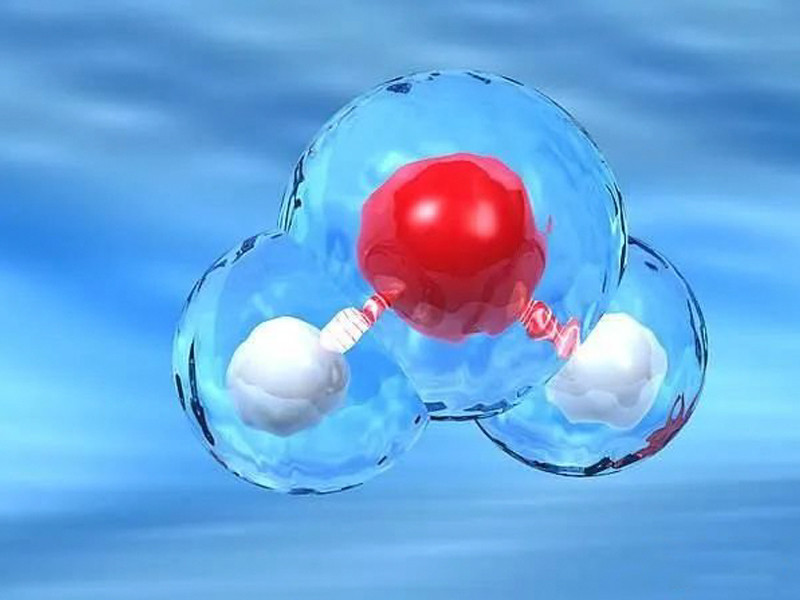
When the bacterial cells rupture, they completely lose their respiratory ability, and dissolved oxygen increases linearly.
Any change in DO value in the fermentation broth is the result of an imbalance between oxygen supply and demand. When the oxygen supply exceeds the oxygen consumption during the fermentation process, the dissolved oxygen concentration increases; Conversely, it decreases.
Therefore, to control the dissolved oxygen concentration in the fermentation broth, it is necessary to start from two aspects: oxygen supply and oxygen consumption.
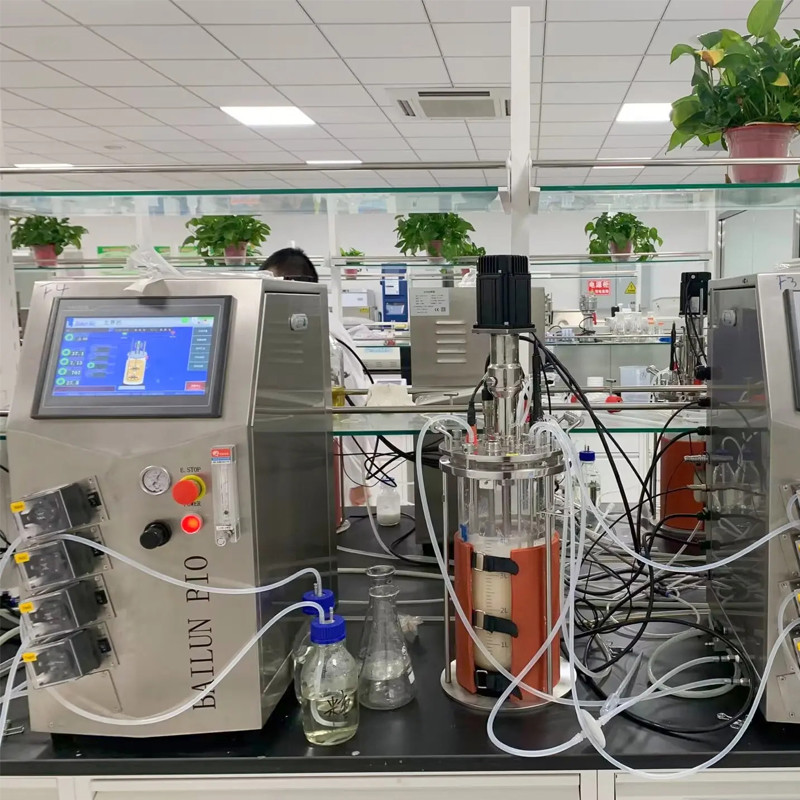
According to the oxygen transfer rate equation OTR=KL α (c * - cL), any factor that can increase KL α and c * can improve the oxygen supply during fermentation.
Therefore, the main approach is to improve the driving force of oxygen transfer and the volumetric oxygen transfer coefficient KL α. The saturation concentration c * of oxygen in the fermentation broth is mainly influenced by temperature, tank pressure, and the properties of the fermentation broth.
And these parameters are already difficult to change under optimized process conditions. Therefore, in practical production, we usually start by increasing the volumetric oxygen transfer coefficient KL α to improve the oxygen supply capacity of the equipment.
In addition to increasing ventilation, it is generally necessary to improve stirring conditions. By increasing the stirring speed or ventilation flow rate, reducing the viscosity of the fermentation broth, etc., the KL α value can be increased to improve the oxygen supply capacity.
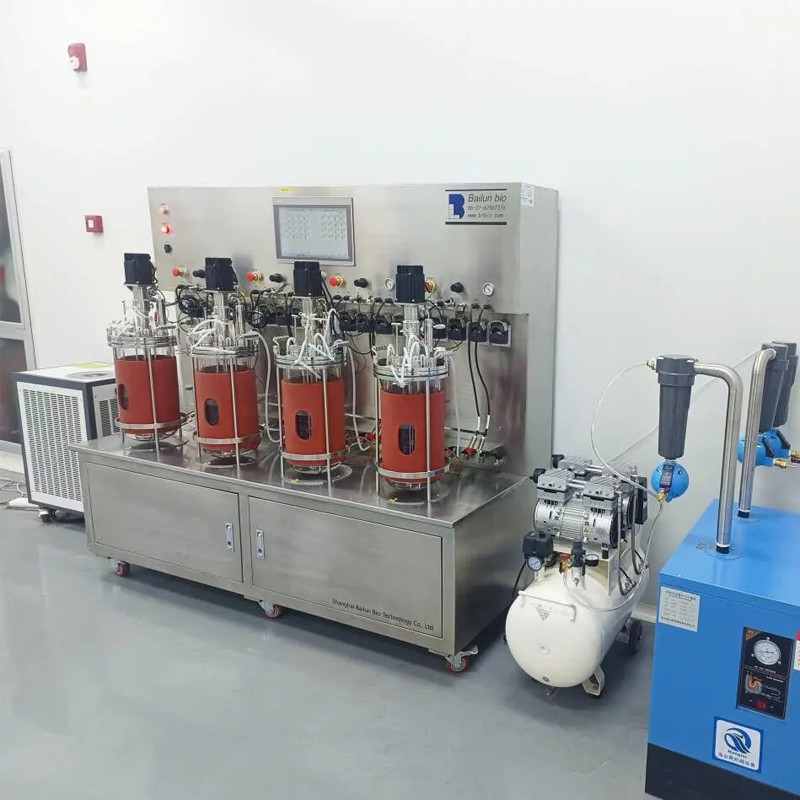
Changing the diameter or speed of the mixer can increase power output, thereby increasing the alpha value.
In addition, changing the number and position of baffles to alter the flow state of the fermentation broth during stirring can also increase the alpha value.
In recent years, the method of increasing the oxygen transfer coefficient of biological applications by adding oxygen transfer intermediates has attracted widespread attention. Oxygen transfer intermediates include hemoglobin, paraffin, etc.
The oxygen consumption during the fermentation process is influenced by factors such as bacterial concentration, type and concentration of nutrient matrix, and cultivation conditions, among which the influence of bacterial concentration is the most significant.
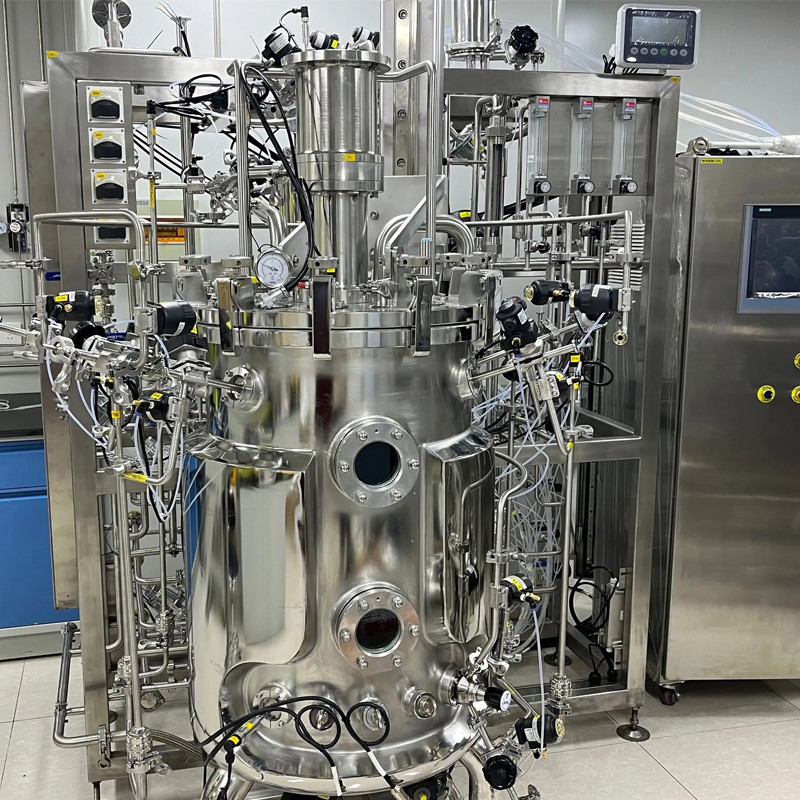
Controlling the specific growth rate of bacteria by the concentration of nutrient matrix, keeping it slightly higher than the critical oxygen concentration for fermentation, and achieving the optimal bacterial concentration, is an important method for controlling the optimal dissolved oxygen concentration.
Penicillin fermentation is achieved by controlling the rate of glucose supplementation to regulate bacterial concentration, thereby controlling dissolved oxygen concentration.
At present, the utilization rate of oxygen in the fermentation industry is still very low, only 40% to 60%, and even lower in the antibiotic fermentation industry, only 2% to 8%.
The growth and metabolic activities of aerobic microorganisms require oxygen consumption, and they can only complete biological oxidation in the presence of oxygen molecules. Therefore, oxygen supply is essential for aerobic microorganisms.