Guidelines for Avoiding Pits in Bioreactors: Incorrect sterilization parameters at 1 ℃ and incorrect selection of stirring blades can result in millions of losses per minute! (including 10 key details)
- Share
- Issue Time
- Apr 22,2025
Summary
As the core equipment of biotechnology, the production and operation details of bioreactors directly affect production efficiency and product quality. Bailun has summarized ten key details based on the latest practice
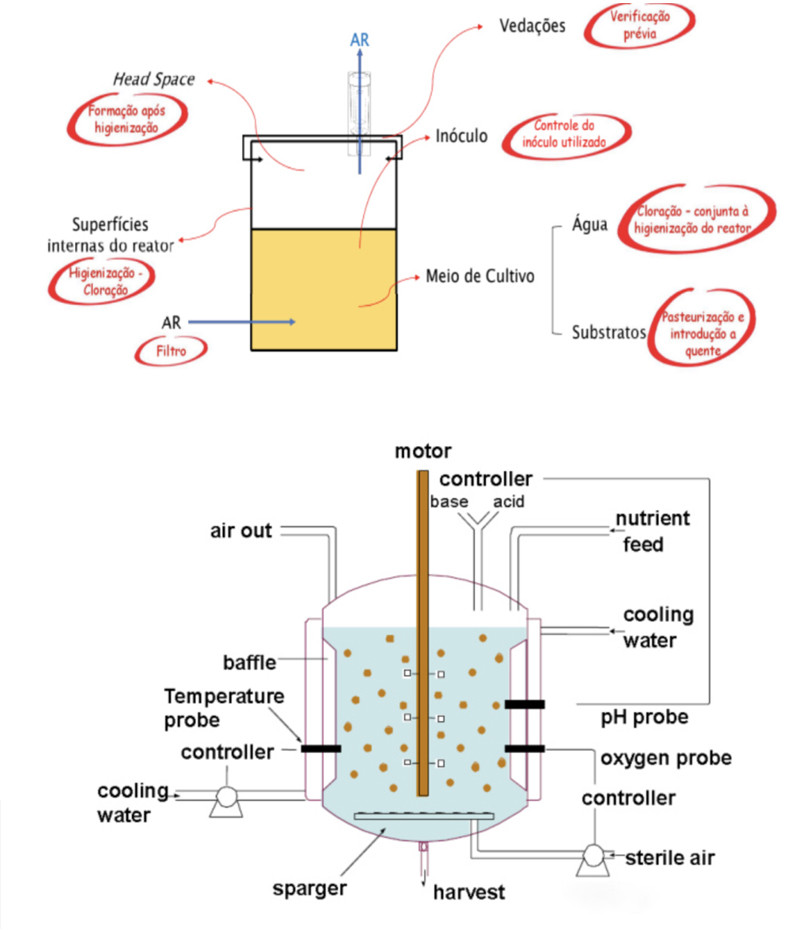
1. Reactor selection should be adapted to process requirements
Select reactor type based on the characteristics of the biological system: mammalian cells require low shear design (such as air lift reactors), while microbial fermentation requires high dissolved oxygen configuration (such as stirred tank reactors).
Disposable reactors (SUB) can shorten project cycles, while stainless steel reactors are suitable for long-term continuous production, requiring comprehensive consideration of cost and cleanliness validation requirements.
2. Material selection and aseptic design
316L stainless steel or borosilicate glass is used to ensure corrosion resistance, and PTFE material is required for sealing to prevent leakage.
Integrate CIP/SIP system (cleaning and steam sterilization) during design to prevent contamination through sterile boundaries (such as plastic trays) and positive pressure operation.
3. Mixing system and shear force control
The mixer design needs to balance mixing efficiency and shear damage: mammalian cell culture uses inclined blades or magnetic stirring, while microbial fermentation uses high-speed turbine stirring.
The baffle setting can eliminate eddy currents and enhance mass transfer efficiency.
4. Multi parameter sensing and automatic control
It is necessary to integrate pH probes, dissolved oxygen sensors, and temperature probes for real-time monitoring of the environment, and achieve automated control through SCADA system.
For example, an oxygen probe is used in conjunction with a jet to dynamically adjust dissolved oxygen, and an overpressure valve ensures operational safety.
5. Precise control of temperature and pH
Use jacket heat exchange devices or external circulating water systems to control temperature (± 0.5 ℃ error). PH control requires the configuration of an acid-base pump and buffer storage tank. Mammalian cells typically maintain a pH of 7.0-7.4, while yeast fermentation requires a lower pH.
6. Optimization of dissolved oxygen transfer efficiency
In a microbial reactor, the aperture and layout of the air distributor affect the dissolved oxygen rate (kLa value). For example, Escherichia coli fermentation requires maintaining a dissolved oxygen saturation of 30% -50%, which can be optimized through gas-liquid mixing (such as membrane aeration) to increase production capacity.
7. Establish a pollution prevention and control system
Before operation, steam sterilization (SIP) is required, sterile membranes are designed for the inoculation port, and a safety sampler is used for sampling to avoid dead volume contamination.
Regular replacement of filters (such as 0.2 μ m sterilization filter cartridges) and monitoring of biological load are required.
8. Optimize the culture medium and improve inoculation
Mammalian cell inoculation density is controlled at 0.5-1 × 10 ^ 6 cells/mL, and fermentation is initiated with Escherichia coli OD600=0.1.
9. Mass transfer and shear equilibrium in amplification process
When scaling up, it is necessary to address the limitations of oxygen transfer and uneven distribution of shear forces. For example, using computational fluid dynamics (CFD) simulation to optimize stirring parameters and ensure consistent volume dissolved oxygen coefficient (kLa).
10. Ensure waste disposal and environmental safety
Configure a waste liquid collection system (such as Allegro MVP virus removal filtration), and condense the fermentation exhaust gas to reduce volatile emissions.