Pilot Platform: Connecting the Key Hub of the "Last Mile" of Biological Manufacturing (with Avoiding Pits Guide and Cost Estimation Table)
- Share
- Issue Time
- May 9,2025
Summary
The pilot platform for biological reactions is a key link connecting laboratory trials with industrial production, and its construction requires comprehensive consideration of various factors such as technology, engineering, regulations, and safety.
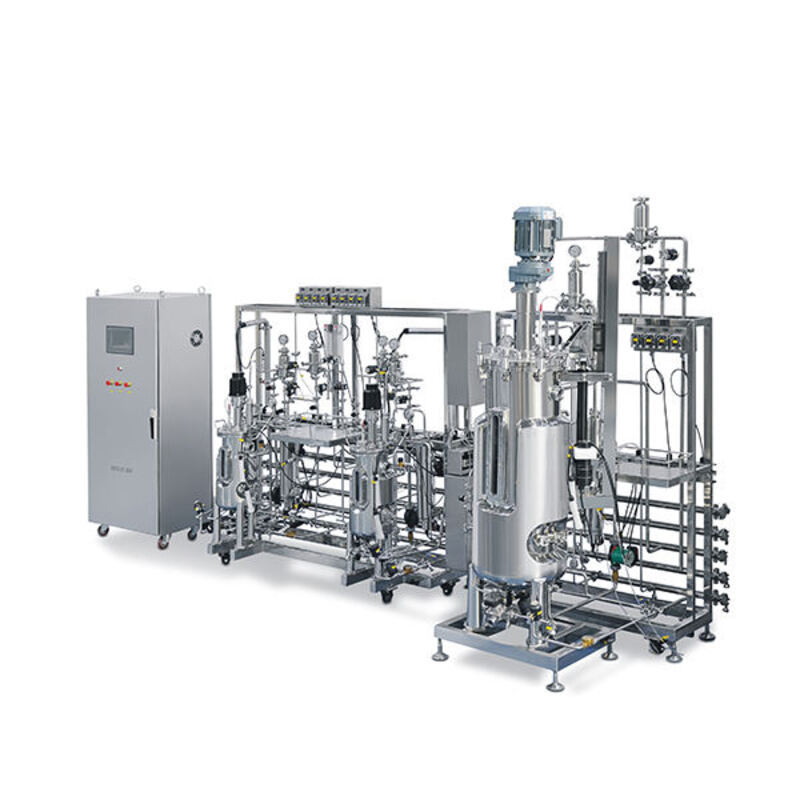
1、 The goal of the pilot platform
1. Validation of amplification process: Verify small-scale process parameters (such as temperature, pH, stirring rate, substrate concentration, etc.) on a pilot scale to address "amplification effects" (such as decreased mass/heat transfer efficiency, and the impact of shear forces on cells).
2. Testing stability and repeatability: Evaluate the stability of biological reactions (such as fermentation, enzyme catalysis, cell culture) during continuous operation, and optimize process robustness.
3. Assessing economic viability: calculating costs such as raw material consumption, energy consumption, and equipment depreciation to provide data support for industrialization feasibility.
4. Verification of compliance: If it involves the fields of pharmaceuticals, food, etc., it is necessary to comply with preliminary compliance tests such as GMP (Good Manufacturing Practice) and GLP (Good Laboratory Practice).
2、 Selecting and designing bioreactors
1. Type selection: Select the reactor type based on the reaction characteristics (such as aerobic/anaerobic, cell culture/microbial fermentation/enzyme reaction) (stirring, air lift, injection, fixed bed/fluidized bed, etc.).
2. Scale matching: The pilot scale is usually 10-100 times that of small-scale trials (such as from 5L small-scale trials to 50-500L pilot trials), and attention should be paid to the amplification rules of geometric similarity, kinetic parameters (such as kLa mass transfer coefficient), and energy input (such as stirring power).
3. System adaptation: PLC/DCS control system needs to be configured to achieve real-time monitoring and feedback adjustment of parameters.
Key parameters include: temperature, pressure, stirring rate, ventilation rate (O ₂/CO ₂), liquid level; pH、 Dissolved oxygen (DO), substrate/product concentration (online monitoring such as NIR, biosensors), and bacterial density (OD value).
三、 Supporting appropriate processes and equipment upstream processes
strain/cell bank management, culture medium preparation and sterilization (online sterilization SIP for tanks/pipelines, culture medium filtration sterilization).
Downstream processes: preliminary separation and purification equipment (such as centrifuges, membrane filtration, and chromatography columns), product collection and storage.
Auxiliary systems: pure water (purified water/injection water), compressed air (sterilization filtration), steam supply, wastewater and exhaust gas treatment (such as activated carbon adsorption, high-temperature sterilization treatment of biological aerosols in exhaust gas).
4、 Ensure regulatory compliance and safety controls
In the fields of pharmaceuticals, food, etc., equipment materials should be selected from sanitary grade materials such as 316L stainless steel, pipeline design should comply with GMP sterile requirements, and online sterilization (SIP) and cleaning verification systems should be configured to ensure batch record traceability.
In terms of biosafety, when it comes to genetically modified organisms, physical containment facilities such as negative pressure workshops and biosafety cabinets need to be set up.
Waste gas and wastewater need to undergo sterilization and inactivation treatment (such as high-temperature sterilization and activated carbon adsorption) to avoid environmental release risks.
5、 Team Capability and Data Management
Bioengineering engineers lead the process amplification, self-control engineers optimize the control system, and quality management personnel ensure compliance records and deviation handling.
In terms of data management, MES system is introduced to achieve real-time storage and audit tracking of process parameters, which complies with electronic record standards such as FDA 21 CFR Part 11, and accumulates a complete data chain for subsequent industrial declaration.