Is the mechanical seal leaking or vibrating? After reading this article, the equipment is as stable as Mount Tai, and the capacity is exploding!
- Share
- Issue Time
- Jul 17,2025
Summary
Mechanical seals are key components in preventing medium leakage in rotating equipment
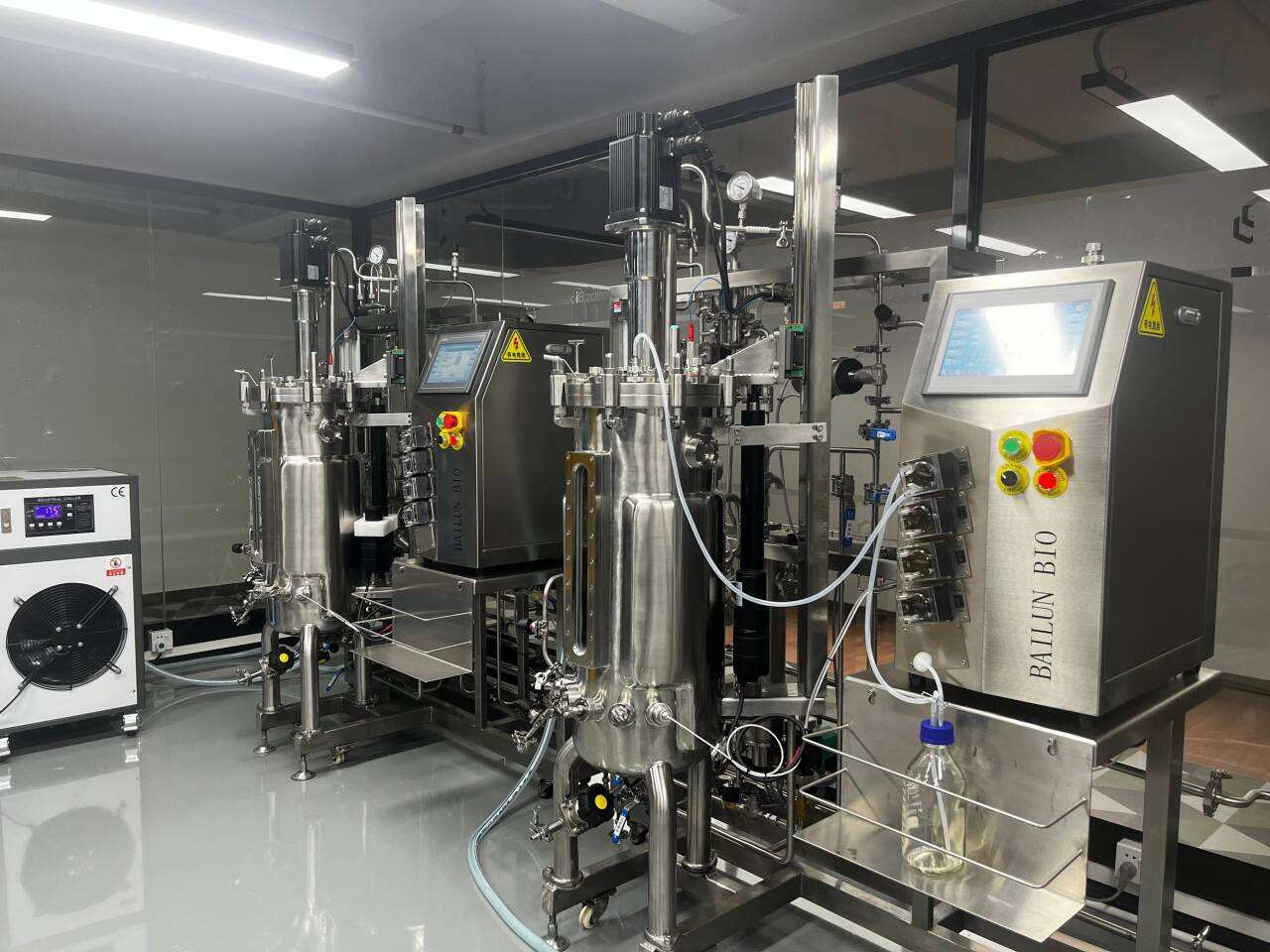
Mechanical seals, as a key component in preventing medium leakage in rotating equipment, have a direct impact on the stability and safety of the equipment during operation.
In long-term use, mechanical seals are prone to various failures due to improper assembly, environmental factors, or design defects. Mastering scientific fault handling methods is crucial to ensuring production efficiency.
1、 Leakage issue
The leakage of mechanical seals is mainly caused by omissions in the assembly process, and precise operations need to be carried out from the source:
Cleanliness control is the foundation. During assembly, all components, tools, and even wiping materials must be kept absolutely clean, especially the sealing end face of the dynamic and static rings, which should be lightly wiped with soft gauze to avoid impurities scratching the precision contact surface (the friction surface width is usually only 2-7 millimeters, and even minor damage may cause leakage).
The edge treatment needs to be fine. The chamfers of the shaft and sealing end cap need to be smoothed, and the relevant rounded corners need to be sanded and polished to prevent scratching the auxiliary sealing ring or hindering the normal fit of the components during assembly.
The assembly of sealing rings requires attention to detail. Rubber auxiliary sealing rings are strictly prohibited from being soaked in gasoline or kerosene to avoid swelling, deformation, or premature aging;
After assembly, it is necessary to manually press the compensating ring to check its flexibility, ensuring smooth axial movement of the moving ring on the shaft, reliable positioning of the elastic opening ring, and avoiding seal failure caused by jamming.
2、 Vibration and heat generation
Vibration and heating are often signals of abnormal friction and require targeted adjustments: insufficient clearance is a common cause. If the gap between the dynamic and static rings and the sealing chamber is too small, it will cause additional friction during rotation.
In this case, it is necessary to increase the inner diameter of the sealing chamber or decrease the outer diameter of the rotation to ensure a safety gap of at least 0.75mm and reserve reasonable space for the components to move.
The adaptability of materials determines stability. Improper pairing of friction pairs can exacerbate wear and heat accumulation.
For example, in high temperature or corrosive media, it is necessary to use temperature resistant and corrosion-resistant dynamic and static ring materials (such as a combination of silicon carbide and graphite) to optimize material properties, reduce friction losses, and suppress heat accumulation.
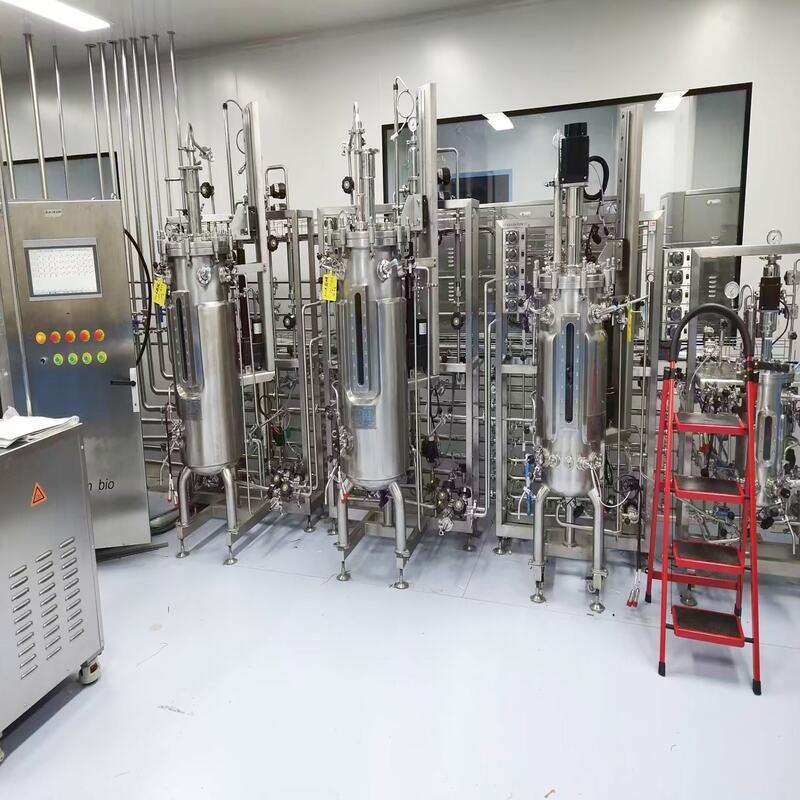
3、 Large displacement of pump shaft
Excessive pump shaft displacement can damage the stable fit of the sealing surface and needs to be solved through structural optimization
For multi-stage centrifugal pumps, the combination design of "balance plate+axial thrust bearing" is an efficient solution:
The balance disk can actively balance axial forces and reduce axial displacement of the shaft;
Axial thrust bearings bear the function of axial limit, effectively eliminating displacement under dual protection, ensuring that the sealing surface always fits tightly.
4、 Pump body vibration
Pump body vibration can indirectly affect the sealing performance of mechanical seals.
During the manufacturing and assembly phase, it is necessary to strictly follow standards and operating procedures to ensure the precision of component processing;
During on-site installation, the positioning of auxiliary equipment such as pumps, motors, bases, and pipelines should be accurately aligned to avoid vibration sources caused by center of gravity deviation or loose connections, and to reduce the impact on mechanical seals at the overall system level.
5、 When the sealing medium contains particles, impurities, or easily crystallizable substances, the auxiliary flushing system becomes a critical protective barrier:
Its core functions include:
Reduce the temperature of the sealing surface by continuously flushing away the heat generated by friction;
Lubricate the friction pair to reduce wear;
Timely wash away particles and crystals in the medium to prevent sedimentation from blocking the spring or scratching the sealing surface, significantly extending the service life of the mechanical seal.
When dealing with mechanical seal failures, it is necessary to consider both its own performance and external environmental influences - paying attention to the machining accuracy and assembly quality of the seals, as well as the synergistic effect of related components such as pump bodies and pipelines.
Only through scientific analysis and targeted adjustments can the efficiency of mechanical seals be maximized, ensuring long-term stable operation of equipment.